If you’re developing a medical device that needs to be worn on the body—whether it’s to support an LVAD, insulin pump, or mobile monitoring unit—then you already know that function isn’t enough. Comfort, discretion, accessibility, and safety are just as critical. That’s where we come in.
At our U.S.-based sewing facility, we specialize in manufacturing medical device-friendly vests—garments that make wearing a medical device, comfortable, and convenient. With over 30 years of experience and a team of 180+ skilled professionals, we’ve been behind some of the most discreet wearable medical applications on the market.
🏁 Where It All Started
Our journey into medical device garment manufacturing began in the early 1990s, when we were approached at a trade show by a doctor who had invented a wearable heart monitor. That initial prototype grew into a nationally distributed device—and we’ve been manufacturing its vest ever since.
Since then, we’ve supported numerous companies—from early-stage concepts to fully scaled production lines—providing everything from pattern development to volume manufacturing. While non-disclosure agreements keep us from naming most of our clients, our role in the rise of wearable medical apparel is well established.
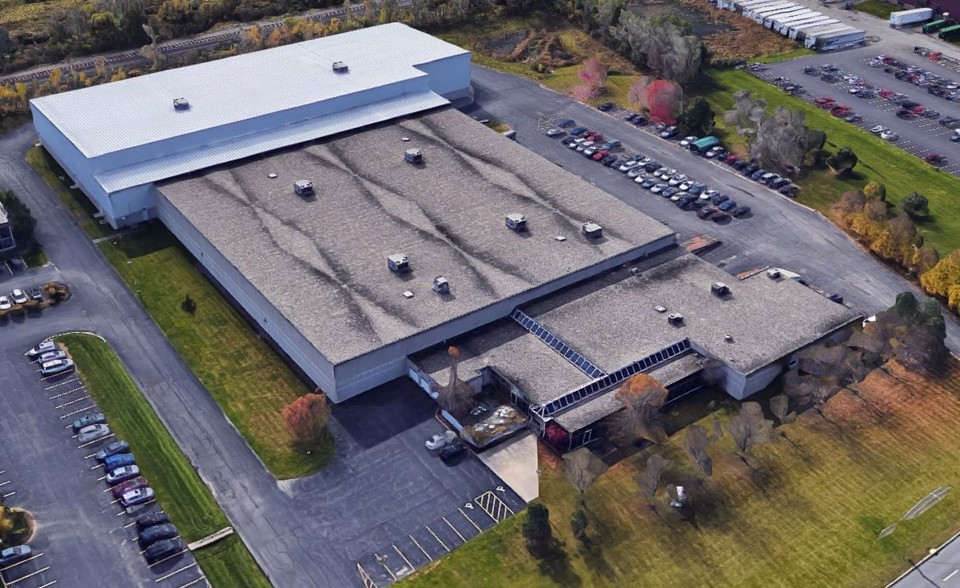
🔧 Why Medical Device-Friendly Vests Matter
Modern medical devices are becoming smaller, smarter, and more mobile—but that doesn’t mean they’re always easy to carry. Patients and professionals alike struggle with how to wear, transport the weight, or conceal devices like:
- Left Ventricular Assist Devices (LVADs)
- Insulin pumps
- Wearable oxygen concentrators
- Ambulatory monitoring systems
Developing a vest solve this problem. They offer a discreet, secure, hands-free solution designed around the device’s unique form factor and the user’s day to day life. A well-designed vest can improve not only comfort and safety but also confidence and mobility.
🧵 What Makes Our Process Different
We’re more than a sewing factory—we’re a custom medical garment partner. Our team works closely with clients to turn initial concepts into production-ready garments, bringing decades of cut-and-sew experience to every stage:
- Concept Review
- Prototyping & Fit Testing
- Design for Manufacturability (DFM)
- Pilot Production
- Full-Scale Manufacturing
This means we don’t just sew—we engineer solutions. Whether your device is wired, wireless, rechargeable, or sensor-driven, we’ll help design a vest that supports its technical requirements while meeting user comfort and wearability standards.
⚖️ Regulatory Awareness: ISO & FDA Familiarity
While we don’t certify products ourselves, we’re highly familiar with the standards medical manufacturers need to meet. Many of the vests we’ve produced have entered markets that required compliance with:
- ISO 13485 (Medical Devices — Quality Management Systems)
- FDA design controls and human factors considerations
- safety, breathability, and washability requirements
We understand how to build to spec while maintaining traceability, consistency, and quality—three pillars of compliance-ready production.
🧠 Case in Point: Innovation from Shark Tank to Walmart
You don’t have to look far to see how mainstream wearable medical apparel is becoming.
- Walmart recently introduced medical device-friendly vests for associates managing conditions like diabetes.
- SCOTTeVEST, a pocket-packed garment company appeared on Shark Tank, has grown a loyal following by integrating device storage into everyday wear.
These cases prove what we already know: wearability and medical tech are no longer separate conversations. And the market for wearable-ready garments is just getting started.
✅ Why Work with Us?
Here’s what you get when you partner with us:
- A team that’s been doing this since before “wearable tech” was a buzzword
- Experience with a wide variety of medical devices and form factors
- Familiarity with regulatory and production-readiness requirements
- Ability to scale production from 10 units to 10,000+
- A commitment to quality, comfort, and confidentiality
We know this industry. We know the stakes. And we know how to build products that people actually want to wear.
🚀 Ready to Start?
Whether you’re building your first prototype or gearing up for national distribution, we’re ready to help you bring your vision to life.
Get in touch today to schedule a consultation, or request a quote for your custom medical device vest.
Let’s build something wearable—and powerful—together.