Industrial sewing is the backbone of mass-producing rugged, high-performance fabric products. If you’ve ever wondered how military-grade backpacks, emergency medical bags, or tarpaulin truck covers are produced at scale, the answer lies in industrial sewing. It’s a world apart from what most people think of when they hear the word “sewing,” and at Fieldtex, it’s our specialty.
We define industrial sewing by its machinery, materials, and manufacturing scale. It’s what separates a hand-stitched tote from a military radio pack that must survive desert deployments and harsh environments. In this article, we’ll explain the differences between industrial and traditional sewing, clarify what makes sewing “industrial,” and highlight how our expertise in medical and military sewn products supports some of the most demanding applications in the world.
Industrial Sewing vs. Garment Manufacturing
While both involve stitching fabric, industrial sewing and garment manufacturing serve very different purposes. Garment manufacturing focuses on clothing and textiles designed for wear shirts, pants, dresses, and accessories. These items often prioritize aesthetics and comfort, using lighter materials like cotton, rayon, or polyester blends.
Industrial sewing, on the other hand, deals with heavy-duty fabrics and functional products. We’re talking about things like ballistic nylon tactical gear, reinforced carrying cases for heavy equipment, and multi-layered medical supply packs. These products must meet strict standards for durability, water resistance, abrasion tolerance, and weight-bearing capacity. It’s not about looking good, it’s about holding up under pressure.
Factory Sewing vs. Home Sewing
The contrast between factory sewing and home sewing is night and day. While home sewing is typically done with a single machine in a spare room or craft area, factory sewing requires a production floor filled with equipment, technicians, and processes.
Home sewers might make pillow covers, hem pants, or create unique one-off items. These are valuable skills, but they don’t scale. When a company needs to produce thousands of tactical pouches for a military contractor, home sewing simply can’t deliver.
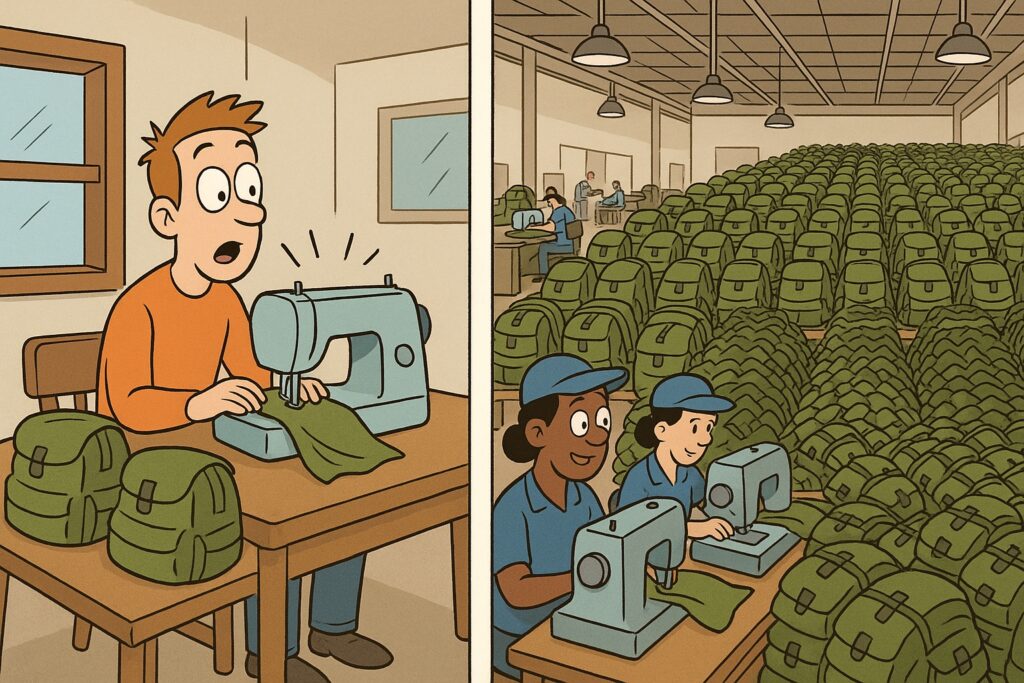
Factory sewing involves:
- Production lines where operators perform specialized tasks
- High-output scheduling for large batch production
- Automated and semi-automated sewing systems
- Quality control systems to ensure every item meets standards
At Fieldtex, we’ve optimized our production floor for efficiency and consistency. A well-organized line allows multiple operators and machines to work on the same product simultaneously, ensuring uniformity and reducing production time.
Industrial Sewing Machines vs. Home Machines
You can’t fill a warehouse with $500 home machines and expect them to sew through layers of ballistic nylon or vinyl for very long. Industrial sewing machines are built differently—and they’re priced accordingly.
- Power & Durability: Industrial machines feature motors that produce significantly more horsepower. This enables them to punch through thick, layered materials without strain or overheating.
- Materials Compatibility: They are designed for heavyweight fabrics and materials like Cordura, Kevlar, vinyl, and canvas.
- Needle and Thread Handling: These machines use large needles and industrial thread types that withstand much more tension and abrasion than standard home equipment can handle.
- Cost & Automation: Entry-level industrial machines start around $3,000, but some of our automated systems on the production floor cost over $45,000. Our industrial fabric cutting systems alone can exceed six figures—but they are essential for precision and volume.
In short: home machines are for crafting. Industrial machines are for battle-ready, field-tested products.
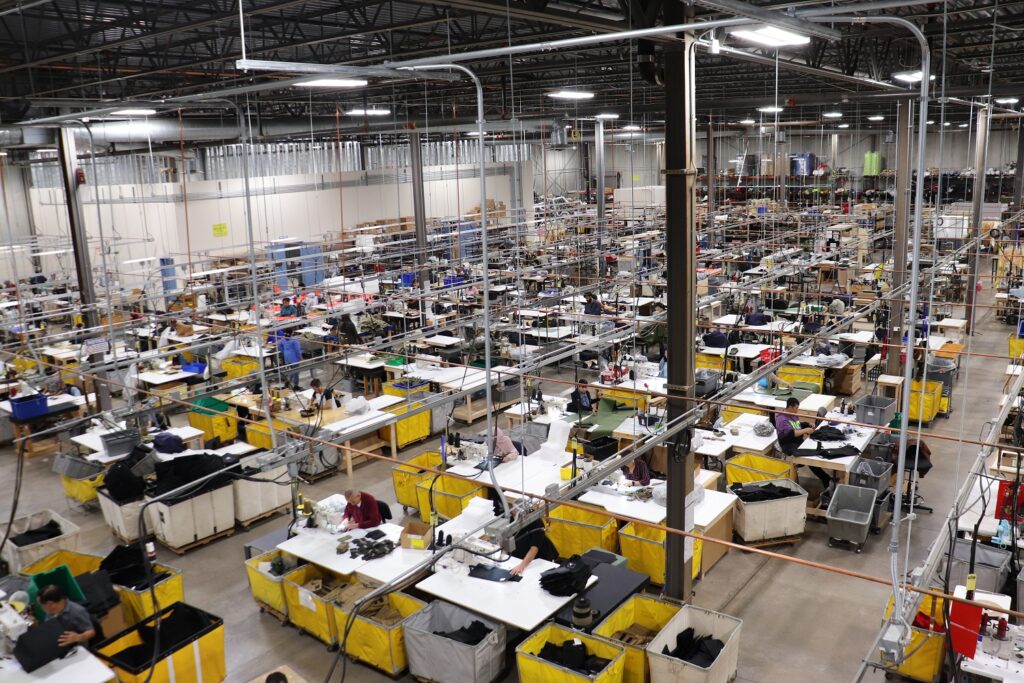
Types of Industrial Sewing Machines We Use
Different jobs require different tools, and the same is true for industrial sewing. At Fieldtex, we use a variety of specialized machines tailored for durability, efficiency, and high-volume output.
- Walking Foot Machines: These machines feed both the top and bottom fabric layers evenly, making them ideal for sewing thick or layered materials like ballistic nylon, vinyl, or webbing. They reduce fabric shifting and are essential for products like trauma kits, tactical belts, and heavy-duty carrying cases.
- Bar Tack Machines: Used to reinforce stress points, bar tackers create dense, short zig-zag stitches in high-tension areas—think backpack shoulder straps, MOLLE webbing, or load-bearing loops. They’re a key component of MIL-SPEC compliant products.
- Programmable Pattern Tackers: These are our most advanced machines—some costing over $45,000. They’re capable of repeating complex stitch patterns with precision and speed, which is invaluable for OEM projects requiring detailed reinforcement or exact replication across large product runs.
These machines allow us to produce reliable, durable sewn products that hold up under real-world stress—whether in the field or in emergency scenarios.
What Products Require Industrial Sewing?
Industrial sewing is most commonly used in the manufacturing of:
- Military backpacks, MOLLE pouches, and tactical belts
- Medical bags and trauma kits
- Custom carrying cases for OEM electronics and tools
- Equipment covers, tarps, and transport gear
- Utility belts, harnesses, and industrial safety gear
These products require exacting standards and consistent quality over large production runs. At Fieldtex, we sew to commercial specifications as well as government and military standards like MIL-SPEC.
Custom Sewn Products for OEMs
Many of our clients are Original Equipment Manufacturers (OEMs) that require sewn components to go with their core products. For example, one of our clients produces military radios. They rely on Fieldtex to design and manufacture all the backpacks, pouches, and cases their gear ships with.
We work closely with engineering teams to develop prototypes, select materials, and test the performance of sewn components under simulated real-world conditions. Whether you need soft-sided cases, protective housing, or holsters to complement your technology, we deliver consistent, field-ready sewn parts at scale.
Why Choose a Contract Sewing Manufacturer?
Choosing a contract sewing manufacturer like Fieldtex means getting more than stitching you get:
- A n in house design and prototyping department
- Access to specialized materials and sourcing
- Certified quality assurance for every batch
- Scalability from dozens to thousands of units
We don’t just make things that look good. We make things that survive drop tests, weather, stress, and deployment.
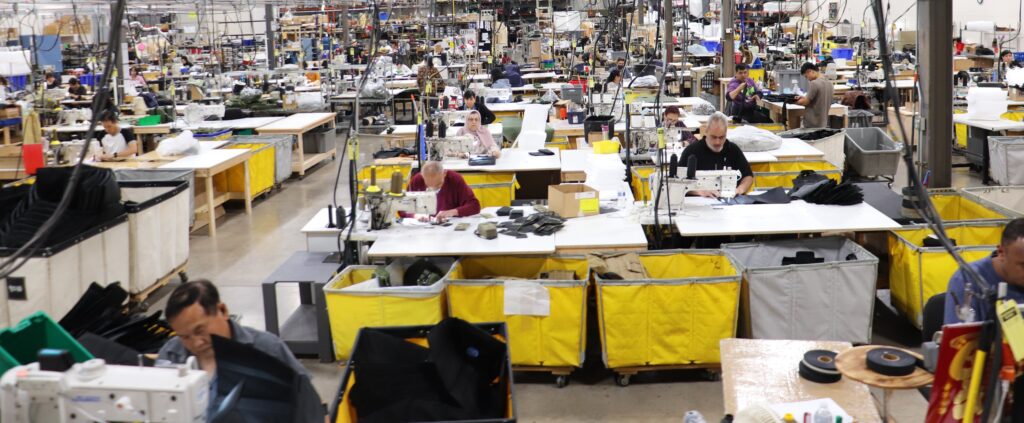
Final Thoughts
Industrial sewing is a world of horsepower, heavy-duty materials, and high-volume production. It isn’t glamorous, but it’s essential. Whether you’re an OEM seeking custom-sewn products or a company that needs production at military standards, working with a true industrial sewing company ensures you get products that perform.
At Fieldtex, we bring decades of experience, a factory full of top-tier equipment, and a focus on functional sewn solutions. If your product needs to be strong, smart, and scalable—it needs industrial sewing.
The best way to mass-produce a fabric product – when you are not equipped with the proper machinery – is to work with a Contract Sewing Manufacturer. This not only allows you to maximize time on other aspects of your business plan, but it also ensures a consistency of product quality and expedited turn around time. Depending on the product that you are producing, the contract sewing process may be more involved to improve durability or meet certain standards. At Fieldtex, we are able to sew commercial grade products as well as conform to military standards and specifications.
“Industrial sewing” refers to the sewing processes used by contract sewers or manufacturers who mass-produce sewn products. This type of sewing is far more complex than using a traditional sewing machine, and often involves a lot of preparation on the part of the pattern maker or designer. Cutting and sewing different fabric elements of a project to create precision-aligned and wrinkle-free products requires a skilled prototype and design department, and repeating this process for mass production takes skilled machinery and operators.
Prior to beginning the sewing process, extensive calculations and measurements need to be taken in order to make sure that the dimensions will be accurate not only when we cut the fabric, but also when the project is constructed. Being conscious that different types of fabric will react differently to seaming and applied thread tension is also beneficial to this process.
Production and Machinery
We utilize the most efficient way to produce a sewn product – working in a production line. A production line involves the materials traveling from station to station, and having many different people work on the same product, performing specific actions to contribute to the product. This results in the sewers performing the same action on each fabric section (lending to both efficiency and quality consistency). Based on the established production sequence, we have organized our industrial sewing machines throughout the factory in an order that makes sense.
Learn about more of our Manufacturing Capabilities here.
If you’re confused and want to get your questions answered, read our FAQ section.
Industrial sewing machines are most often programmed to repeat one action over and over again, at a far faster speed than someone sewing on an in-home sewing machine and often with more precision. We have several industrial sewing machines in our factory, programmed to perform specific actions and sew specific pieces of each project – for example, a machine programmed to stitch a certain box tack, and another machine designed to stitch a bar tack. By using both an efficient floor plan, state-of-the-art industrial sewing machinery, and a skilled prototype and design department, we are able to mass-produce even custom patterned sewn products from OEMs.